Double End CBN Grinding Wheels Customer Case Background
Our customer uses a Wendt WBM 221 grinder in the field of high-precision metal processing, focusing on face grinding of PCBN (Polycrystalline Cubic Boron Nitride) inserts. In order to meet the demands of machining high hardness materials, the customer needed efficient grinding tools and wanted to optimize the grinding process to improve productivity and machining quality.
Recommended products:
Double-ended CBN grinding wheels
In order to meet the customer's requirements, we recommend the use of double-ended CBN grinding wheels, the detailed specifications of which are listed below:
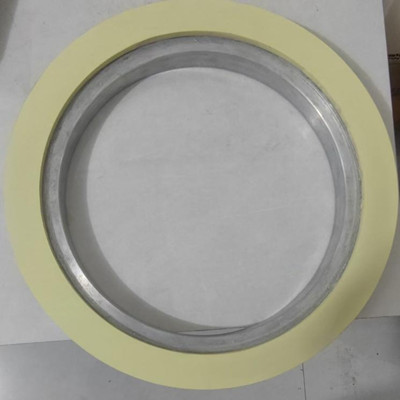
Grinding machine model: Wendt WBM 221 (oil cooled)
Grinding wheel size: Ø 350 mm, H = 260, bond = 30 x 6.1, T = 32
Grinding process: PCBN insert face grinding, CBN with 60/40% solid carbide
Maximum removal volume: 0.05-0.08 mm
The wheel design was developed for efficient grinding of PCBN materials. The ratio and structure of the bond ensures excellent grinding performance and durability to meet the challenges of machining high hardness materials.
Machining process and performance
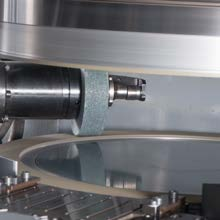
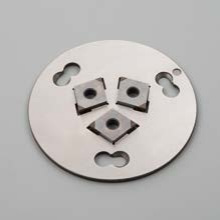
During machining with the Wendt WBM 221 grinder, the customer utilized the recommended double-ended CBN grinding wheels for face grinding of PCBN inserts. During the grinding process, the customer set a maximum removal volume of 0.05-0.08 mm, which significantly improved the grinding efficiency. The oil cooling system effectively reduces the heat accumulation during the grinding process and further improves the grinding accuracy and surface quality.
In the actual test, the customer found that the grinding stability and consistency were significantly enhanced after using double-ended CBN grinding wheels, which can meet the strict requirements of high-precision machining.
Customer Feedback of Double End CBN Grinding Wheels
The customer highly evaluated the performance of the double-ended CBN grinding wheels, especially in the machining of high hardness PCBN inserts, the wheels showed excellent wear resistance and machining efficiency. The customer stated that by using the grinding wheel, their productivity has been significantly improved and grinding costs have been reduced. Due to the satisfactory test results, the customer decided to continue using our products in future production.
Conclusion
This case demonstrates our technical competence and market adaptability in high-precision grinding solutions. By providing our customer with customized double-ended CBN grinding wheels, we not only solved their grinding process challenges, but also improved the overall machining efficiency and quality. In the future, we will continue to dedicate ourselves to providing our customers with high-performance grinding tools to help them stay ahead of the competition.