1.Machine Technical Specifications Basic specification of High Precision CNC Cylindrical Grinding Machine:
Center height/maximum grinding diameter: 320mm
Distance between two centers: 500mm
Maximum workpiece weight between the two centers: 60kg
Maximum diameter of grinding wheel: CBN grinding wheel φ510mm
X axis /Z axis (X axis is configured with linear motor and HEIDENHAIN) travel/fast speed: 350mm/15m/min
X axis /Z axis minimum resolution 0.0001mm
Grinding wheel spindle type/Maximum linear speed: ball bearing electric spindle /100m/sec
CNC system: Siemens 828D grinding machine version
Software technology of High Precision CNC Cylindrical Grinding Machine:
Fully graphical programming
Simple and easy to use
Quick setting saves operation time
Modular grinding and finishing cycle
Various functions, suitable for ISO programming
CAD/CAM software extension
Structural characteristics of High Precision CNC Cylindrical Grinding Machine:
Good rigidity bed structure
High precision high speed ball bearing motorized spindle
High bearing capacity of plastic precision shovel table
X axis/linear motor plus HEIDENHAIN 50 nm grating scale feedback
Special rotary precision workpiece head frame, spindle telescopic
Double spindle double drive structure
Flexible options configuration
Stable and strong cast iron lathe
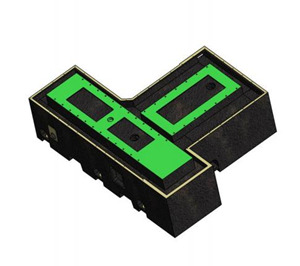
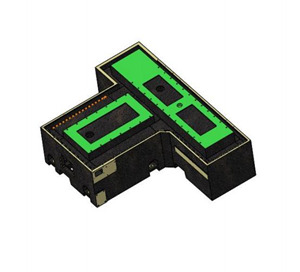
Design characteristics of the lathe bed and main components
In the grinding process, the most important thing we need is to maintain accuracy. The maintenance of accuracy is far more dependent on thermal stability than vibration resistance. Cast iron itself has a very low coefficient of thermal expansion, and more importantly, cast iron has a very high heat conductivity compared to artificial granite. Machine will generate large amount of heat during the production process, which can be quickly and evenly transmitted through the cast iron lathe bed, so that the machine can maintain an extremely stable state.
Key components on the machine such as grinding wheel head, workpiece head, tail, spindle and all bearing support components are made of high-grade cast iron or steel materials, ensuring a homogeneous, continuous and stable coefficient of thermal expansion between the machine bed and components.
Any occasional short time thermal changes will be compensated by stable composite cast iron, which can provide a more stable environment, better than the main parts of steel, castings and artificial granite structure machine.
In addition, the cast iron structure has the advantages of high rigidity and high seismic performance, and its solid performance is better than that of typical artificial granite structures. Ideal for high precision grinding machines.
Longitudinal (z-axis) and transverse (X-axis) line rails
Longitudinal fully supported line rail
Transverse fully supported line rail
The X-axis adopts Sodick linear motor and HEIDENHAIN grating rule for closed-loop control with high precision, fast response, minimum feed of 0.0001mm, strong load capacity, and can maintain the stability of the mechanism under the condition of high-speed grinding. The whole adopts water cooling mode and is equipped with water cooler, which effectively reduces the influence of temperature on processing accuracy.
Permanent magnet synchronous motorized spindle with high rigidity and high precision
The grinding wheel spindle adopts high-speed ceramic CBN grinding wheel, which is suitable for high-efficiency grinding production in large quantities. The permanent magnet synchronous electric spindle can rotate up to 4500RMP, and the grinding wheel line speed can reach up to 100M/S. It has the characteristics of high rigidity, high precision and high stability. Suitable for large feed grinding, High grinding efficiency.
The working head frame is controlled by servo motor, and the high precision mechanical bearing spindle can be installed with special fixture, and the workpiece can be automatically clamped with the customized center, so as to carry out workpiece turning grinding and realize automatic production.
The dressing spindle adopts high-speed electric spindle with adjustable speed, and the dresser uses sintered diamond roller. Good dressing effect, the spindle adopts vertical installation mode, which can trim the end face and outer surface of the grinding wheel at one time.
The grinding wheel spindle is equipped with imported dynamic balancing instrument, which can balance grinding wheel runout, reduce workpiece vibration, improve spindle service life and anti-collision functions, improve production efficiency and quality, and increase the safety and reliability of the equipment.
Double spindle
Double spindle movable design, servo motor and screw control, with driving function, at the same time can be installed special fixture, with customized center, automatic clamping workpiece, when replacing the workpiece, can control the motor to adjust the stroke.
Control system
CNC grinding software developed jointly by Siemens
1.1. Graphical software is easy to learn 1.2. fast and convenient setting
1.3. 10.4 inch color digital LCD display 1.4. large capacity storage
1.5. No hard disk is more stable 1.6. multi-wheel data management
1.7. remote diagnosis and help 1.8. Ethernet, RS232 interface
1.9, USB and flash memory card storage 1.10. background editing function
1.11. Set a security password
1.12fully customized, to provide cutting-edge user experience efficiency priority software design
The purpose of machine software design is to reduce the setup time, and its purpose is to reduce the finished product of a single piece of production and expand the production volume. The simple setup page guides the operator through a clear user graphical interface to enter pen and wheel data. All programs and settings are displayed graphically, and these graphical programs do not require the operator to enter complex code and subroutines, thus reducing programming time to reduce costs. The system also fully supports ISO programs, and is easy to view and edit, and can be used perfectly with other programs.
After the secondary development of the human-machine interface, with Siemens high-performance servo motor, so that the equipment CNC system and drive system have better compatibility, at the same time, it has automatic sand repair and automatic compensation functions to ensure the stability and accuracy of feed and grinding.(1) The system panel is made of die-cast magnesium alloy, which is strong and durable. System keys with protective film, IP65 protection level.
(2) The system does not need batteries, and the data is permanently stored. No cooling fan required. Motor encoders don't need batteries to remember positions.
(3) USB (online processing) CF card capacity is unlimited, Ethernet interface (through the network disk option can be external computer as a storage, unlimited expansion of program capacity), no need to install any hardware and software. The upper on-line computer can monitor the machine processing. The program in USB and CF card can be edited and modified at will on the CNC system.
(4) Drive the processing cycle of the painting function, which is intuitive and can improve the efficiency of programming processing.
(5) Graphical programming tools shopmill/shopturn. Fast and intuitive programming without G code (option) is especially suitable for small batch workpieces.
(6) High control accuracy of the system and servo driver, nano calculation accuracy of 80-bit floating point number, eliminating calculation errors.