The United Grinding Group is one of the leading manufacturers of precision machine tools for grinding, electrolysis, laser machining, combined machining and measuring. The Group's eight brands are dedicated to different grinding fields: MÄGERLE, BLOHM and JUNG for flat profile grinding, STUDER, SCHAUDT and MIKROSA for internal and external grinding, and WALTER and EWAG for tool grinding. The products of the eight brands are available in the fields of aerospace, automotive, mold and die, medical equipment, rail transportation and tool manufacturing, making them one of the leading companies in the grinding industry.
Comprehensive grinding processing solutions:
The 13 exhibition areas of United Grinding Group showcased products representing the top grinding level and provided effective solutions for customers.
1. WALTER, the originator of the "two-in-one" manufacturing concept
From the production point of view, the two-in-one concept means that users can use the same machine for electrolytic machining of tools (PCD) and grinding of tools (carbide), and more importantly, both processing methods can be performed on the same machine without switching to another machine. without having to switch to another machine, saving a lot of time.
Two new HELITRONIC series were presented, the HELITRONIC POWER DIAMOND 400, a two-in-one machine for electrolytic grinding, and the HELITRONICPOWER, which represents the top quality in the production and grinding of rotationally symmetrical tools worldwide. It is capable of grinding complex geometries in a single clamping. In combination with the available loading system, it sets the benchmark in terms of productivity and flexibility. These properties are highly appreciated by users and have made it the best-selling WALTER series tool grinding machine worldwide.
2. Combining high efficiency and precision - the MIKROSA KRONOS S 250
The KRONOS S 250 centerless grinding machine not only offers high productivity and precision, but also quick changeover, and this machine and equipment processes a wide range of parts.The KRONOS S 250 combines optimized grinding quality with grinding speed in a compact and functional design, with a cross-shaped slide structure on both the grinding wheel and guide wheel side, and a grinding wheel spindle supported by hybrid bearings to achieve a maximum linear speed of 150 m/s on the grinding wheel surface. Good repeatability and high precision of grinding results with controllable tolerance range of ±0.5µm, designed for mass production (simultaneous grinding of multiple workpieces).
3. Handling complex and diverse grinding tasks - STUDER S31
With hundreds of years of grinding experience, STUDER offers reliable programming and efficient operation. This new S31 internal and external cylindrical grinding machine can perform complex and diverse grinding tasks with precision and reliability. The machine is suitable for small and medium-sized workpieces in single, small and large series production with a choice of 400, 550, 1000 and 1600 mm center distances and a center height of 175 mm. The S31 can grind different diameters and cones with one grinding wheel without intermediate dressing.
4. The compact solution - the MÄGERLE MFP 30 grinding center
The new, compact MFP 30 5-axis grinding center is ideally suited for grinding complex geometries, especially the blades of aircraft turbines. For the highly flexible machining of workpieces, the integrated tool changer can be loaded with different tool changers. The powerful spindle drive allows different grinding processes to be combined with robust tool holders for a wide range of machining profiles. The high-speed, high-performance spindle up to 12,000 rpm provides excellent machining conditions for grinding and milling.
5. Excellent dynamic performance and improved performance - BLOHM PROFIMAT XT
Higher axis speed, higher acceleration and higher system stiffness are improved influences that increase the productivity and improve the quality of parts with the PROFIMAT XT. The PROFIMAT XT combines several technologies and can be used for reciprocating grinding and, if equipped with the optional overhead dresser, for IPD and CD grinding.
Moresuperhard grinding solutions for Unitied Grinding Grinders:
Vitrified diamond/CBN grinding wheels:
♦ The bonding strength of vitrified bond to grinding is better than resin bond
♦ After customized diamond grinding tools with higher diamond concentration, it is less heat and jam generate in grinding
♦ High grinding efficiency
♦ Very sharp grinding
♦ Long lifespan and easy to dress
Resin dianond/CBN Wheels
♦ self-sharpening, resin bond wheel is easy to use and is suitable for roughing – finishing.
♦ moderate abrasive holding strength and wear-resistance, this wheel is suitable for roughing with free cutting.
♦ elasticity, this wheel using fine grits is suitable for finishing.
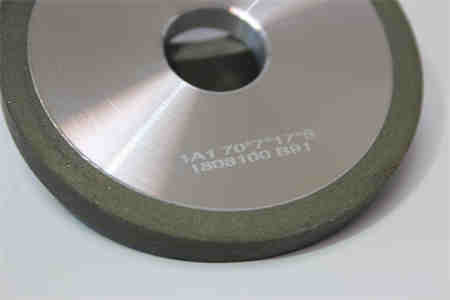
Resin bond CBN grinding wheels are suitable for grinding ferrous metals, such as cast iron, high speed steels, and sintered iron,
processing hard to machine materials, because CBN grains are much stronger than conventional abrasives and can perform precision
grinding because they wear much less than conventional abrasives.