New Energy Vehicle Market Analysis:
China from the world: China's new energy vehicle production will account for more than 50% of the total global new energy vehicle market in 2021, having become the largest new energy vehicle market.
The new energy vehicle industry report released in mid-2022 by the China Association of Automobile Manufacturers raised its annual production forecast to 5.5 million units in 2022.
The growth trend of pure electric vehicles is stronger than that of plug-in hybrid vehicles. Meanwhile the supply chain of auto parts is reshuffled due to the impact of the new energy vehicle market.
From split components to 3-in-1 electric drive system is the mainstream of the current market, and the market also shows a clear trend of all-in-one.
Industry chain changes and upgrades in the industry chain upstream and downstream conduction, on the one hand, the vehicle manufacturers are accelerating the layout of the industry chain of key components, on the other hand, the traditional parts manufacturing also continue to technical innovation, through technical cooperation with the vehicle manufacturers to maintain close cooperation. At the same time, there are new entrants in the market, such as Huawei. Regardless of what kind of electrification technology path (pure electric, plug-in hybrid, booster, etc.), or what kind of power battery (lithium iron phosphate, high nickel ternary, fuel cells, etc.), the electric drive system is the "heart" of the new energy vehicle, responsible for converting electricity into kinetic energy, providing power output and control.
The main requirements of shaft parts processing:
▪ High precision
▪ Automation
▪ Process optimization
▪ Flexibility
▪ Stability
▪ Reliability
Currently, there are three main types of motor shafts on the market:
solid shafts,
hollow shafts and
semi-hollow shafts.
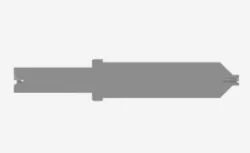
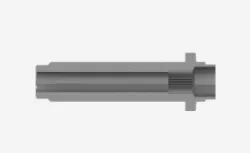
New energy vehicle motor shaft grinding solutions:
Moresuperhard's qualified CBN grinding wheels
■High-speed grinding with linear speed up to 140 m/s
■Increased productivity by grinding diameter + endface without tool change or B-axis rotation
■Maximum flexibility. Base changeover time can be reduced by 70%, eliminating the need to change wheels for each workpiece!
■The perfect balance of efficiency and cost with straight grinding wheels for face grinding