High precision diamond rotary grinding wheel
high precision diamond rotary grinding wheel for the desired grinding application. Also available are CNC dressing wheels with PCD or natural diamonds and gear grinding wheels or custom-built diamond tools for grinding of CBN wheels.
The plunge dressing method has higher requirements for the manufacture of diamond rollers, especially when grinding workpieces with a small number of teeth. On the one hand, the fewer the number of teeth, the smaller the root circle, the larger the contact area of the R arc of the roller when dressing the grinding wheel, and the higher the requirements for roller manufacturing; on the other hand, the less the number of teeth of the workpiece, the smaller the radius of curvature of the involute, and the greater the contact area of the roller’s R arc when dressing the grinding wheel. The profile has a high degree of curvature and is sensitive to radial errors, which puts forward higher requirements for the radial runout error of the roller itself and the dynamic radial runout error after installation.
According to the cutting-in dressing principle, CNC gear grinding machine manufacturers have developed their own unique grinding wheel dressing devices. According to the dressing characteristics, they can be divided into two types: single roller and double roller. The single roller has simple structure, small volume and small trimming range. When dressing large modulus and large tooth depth, it is necessary to make a diamond roller with a large diameter. The rigidity of the roller is poor and it is easy to interfere with the workpiece. At present, the maximum modulus that can be trimmed with a single roller is 25, and the above-mentioned problems can be effectively avoided by using double rollers for trimming. One roller can dress one side of the grinding wheel, the modulus of dressing is not limited, it can be trimmed with a small roller, and the rigidity is good. It is common to use single-roller dressing on small and medium-sized forming wheel gear grinding machines, and double-roller dressing is commonly used on large-scale gear grinding machines.
Swing type roller dressing
The dressing structure of the oscillating diamond roller is relatively complicated, and five actions need to be realized: wheel rotation, diamond wheel rotation, diamond wheel swing, roller and wheel offset, and dressing feed. With this method, the diamond roller section is always in the normal section of the sand contour, and only one point on the arc of the diamond roller R is used to dress the grinding wheel, similar to the use of a diamond nib to dress the grinding wheel.
Using this dressing method, the wear of the roller has little effect on the accuracy of the sand profile. When wear occurs, the radius of the roller R arc can be modified to adjust the position of the contact point to achieve compensation. The point-contact dressing reduces the requirements on the contour accuracy of the rollers, but the abrasion is aggravated. Normal contact dressing is not affected by the curvature radius of the workpiece profile, and is suitable for workpieces with a small number of teeth. In order to improve the accuracy, the radius of the R arc of the roller should not be too large. The roller adopts a single-arc disc structure, which is light in structure, has many moving links and is slightly less rigid. It is suitable for the dressing of small workpieces. See figure 7 for the trimming of the swinging roller.
Coordinate trimming device
The polar coordinate dressing device combines the characteristics of plunge dressing and swing dressing. The numerical control system controls the plane motion of the diamond roller in the polar coordinate system to envelop the section curve of the grinding wheel shaft to realize the shaping and dressing of the grinding wheel. When dressing the grinding wheel, the dressing roller and the grinding wheel rotate around the center of rotation at a certain linear speed ratio. The grinding wheel swings around the swing center, and the dressing roller moves linearly toward the grinding wheel along its own radial direction. The cross-section of the grinding wheel is trimmed into a shape suitable for the tooth space of the gear to be ground through two-axis interpolation of the linear axis and the rotary axis.
During the dressing process, the normal vector at the contact point between the grinding wheel and the roller is always the same, and the relative velocity vector at this point is perpendicular to each other. Two-axis interpolation, which occupies a small space, is suitable for the dressing of grinding wheels used in large internal gear grinding devices. However, this method can only be trimmed with a single roller, and the modulus that can be trimmed is limited, and it is not suitable for the dressing of formed grinding wheels for grinding gears with large modulus and large tooth depth.
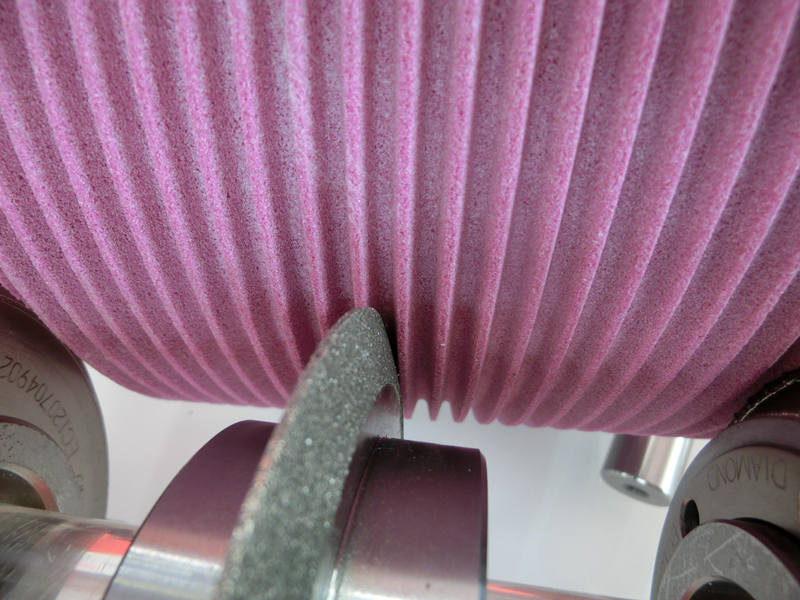