Rotary diamond dresser for gear profile grinding
Rotary diamond dresser method of CNC forming grinding wheel gear grinding machine
Analysis of diamond pen and diamond roller trimming and controlling forming gear grinding machine. CNC forming grinding wheel gear grinding machines are widely used in the precision gear grinding of heavy machinery transmission industries such as aerospace, shipbuilding, wind power, nuclear power, military industry, etc., especially suitable for precision grinding of gears with large modulus and small number of teeth. Grinding gears with a profiled grinding wheel gear grinding machine trims the section of the grinding wheel into a shape suitable for the tooth groove of the gear, and obtains a precise tooth profile through reciprocating grinding. The biggest advantage of the CNC forming grinding wheel gear grinding machine is the CNC grinding wheel dresser, equipped with the corresponding software, it can grind various tooth profile trimmings, tooth root fillet transition curves, drum teeth, various special tooth profiles, and cycloid teeth. , Arc teeth and splines, etc.
The CNC forming grinding wheel gear grinding machine adopts the forming method to grind, and the section accuracy of the grinding wheel is the key, which depends on the section calculation accuracy and the grinding wheel dressing accuracy. Domestic and foreign gear grinding machine manufacturers have conducted in-depth research on the shaping wheel dressing technology and developed different grinding wheel dressing devices to ensure the dressing accuracy of the grinding wheel and improve the gear grinding accuracy. This article introduces the progress of the grinding wheel dressing technology of CNC forming grinding wheel gear grinding machine and the existing CNC grinding wheel dressing device and dressing technology, and discusses how to obtain high profile accuracy.
Grinding method of CNC forming grinding wheel gear grinding machine
There are two main types of dressing for forming grinding wheels: diamond pen and diamond roller. The dressing structure of diamond pen is simple, and the cost is low. In theory, higher dressing accuracy can be obtained. Because the diamond pen is severely worn, short in life, and difficult to estimate, it cannot be accurately compensated, resulting in poor consistency of sand contour accuracy, which has a greater impact on the grinding of large gears, and is gradually replaced by diamond roller dressing. The diamond roller has high rigidity, large amount of dressing, and high efficiency. It adopts the trajectory envelope method, which is more suitable for dressing complex forming surfaces. Diamond roller dressing methods are divided into plunge-type roller dressing and swing type roller dressing.
Cut-in roller dressing
When using plunge-cut roller dressing, the diamond roller rotates at a high speed under the drive of the dressing motor, and performs a cutting movement along the radial direction of the grinding wheel. In order to dress the forming surface, the diamond roller and the grinding wheel move relative to each other in the axial direction. A certain linear speed ratio revolves around its own center of rotation. The grinding wheel reciprocates along its own axis (Y-axis), and the dressing roller follows its own radial (W-axis) direction in a certain proportion to follow the axial movement of the grinding wheel. The Y-axis and W-axis interpolation follow the arc or straight line, and the diamond roller R arc center follows the sand contour equidistant line. Use the contact point of the roller and the grinding wheel to envelop the section of the grinding wheel.
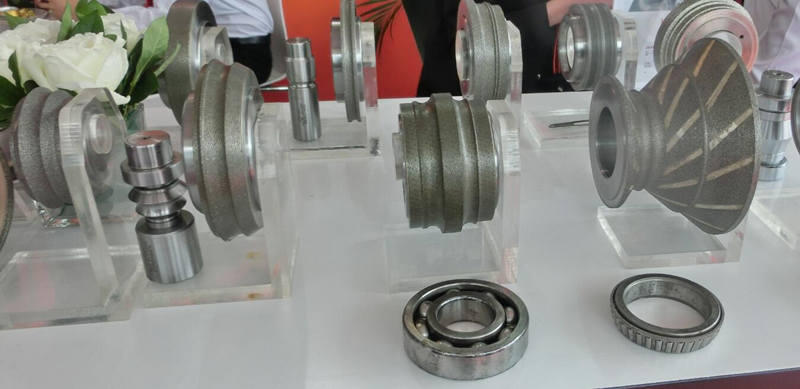