What is servo grinding?
The servo grinding, also called tangential point tracking grinding and following type grinding, is proposed for the grinding of complex rotary parts of crankshafts. When grinding the connecting rod neck, the workpiece is positioned at the center of the spindle neck (C-axis) and rotates around it, and the grinding wheel reciprocates along the horizontal direction (X-axis) to ensure that the grinding wheel is always tangent to the connecting rod neck, thus completing the grinding process.
Since this grinding method can process both round and non-round workpieces, such as various cams, camshafts, eccentric shafts, crankshafts and various curved surfaces and polygonal parts of the CNC grinding technology. Especially in the grinding of crankshaft, it realizes one clamping to complete the grinding of crankshaft connecting rod neck and spindle neck, improves the processing accuracy, and solves the problem of relying on the traditional fixture with poor flexibility, long adjustment cycle and low accuracy.
At present, domestic and foreign automotive field of CNC servo grinding machine tools, whether it is processing crankshaft connecting rod neck or cam, most of the C-X crankshaft follower grinding structural principle; the development of direct-drive technology and the mature application of hydrostatic pressure technology to solve the follower of the high dynamic responsiveness of the mechanism; high-speed CBN grinding wheel grinding technology, not only to improve the efficiency of the grinding process, due to the reduction of wear of the grinding wheel, and at the same time to improve the precision of the grinding process. The development of CNC technology improves the accuracy of follower curve fitting, and the learning function of the CNC system optimizes the machining program.
Technical Difficulties and Key Technologies of Servo Grinding:
1. The tangential tracking grinding process puts forward very high requirements on the high-speed dynamic response characteristics of the grinding wheel holder: object-oriented optimization method of tangential tracking grinding electromechanical matching must be researched to improve the high-dynamic response characteristics of the grinding wheel holder; research must be carried out on the variable-speed drive based on the grinding load, servo characteristics and constant wear removal rate in order to meet the high requirements of the grinding process accuracy and efficiency; research must be carried out on the online measurement of the machining error process It is necessary to study the process of on-line measurement of processing error control method and determine the efficient automatic on-line compensation strategy and process method to ensure the grinding efficiency and precision.
2. Technical difficulties originated from improving the reliability of the whole machine and service life of key components: under the long-term, high-efficiency processing and continuous operation of the production line, high requirements are put forward for the reliability of the whole machine and the service life of key components of the CNC crankshaft grinding machine. In view of the high requirements on the spindle system's rotational speed, support stiffness and dynamic balance, we study the influence of different support and drive methods on the performance of high-speed spindle system; we study the key issues such as the design and manufacturing technology of double cross slide feed system, double cross slide drive and support technology; and we study the forms of failure and influencing factors of the key components of the crankshaft grinding machine.
3. Technical difficulties originated from the demands of engine production line of automobile OEMs: The production capacity and process flow planning of engine production line of automobile OEMs put forward high requirements on the production beat, process mode and optimization of margin allocation of crankshaft grinding machines. In view of the production capacity and process planning requirements of the engine production line of automobile OEMs, the crankshaft grinding machine configuration strategy for the engine production line of automobile OEMs is studied; and under the premise of double wheelheads, the high efficiency grinding process is studied by taking into account the factors of grinding efficiency, machining accuracy, structural rigidity and cutting deformation.
Moresuperhard Servo Grinding Machines in the Automotive Field
With hydrostatic liquid suspension electric spindle, high rigidity, high speed, low vibration, high grinding force.
►
Servo Surface CNC cylindrical grinder Models
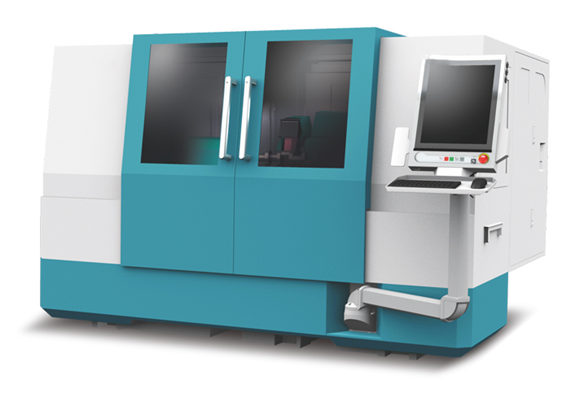
GP32
J2
►Applications:
- automotive and aerospace industries,
- tool manufacturing
- die makingn
Moresuperhard machine tools are designed for the multi-stage structure of crankshaft main and connecting rod journals, as well as the requirements of tangential point tracking grinding, comprehensive grinding efficiency, processing accuracy, processing flexibility and production cycle, etc., taking into account the structural rigidity and cutting deformation, to formulate a dual grinding wheel holder follower grinding process program; crankshaft production line grinder with independent follower motion control function, combined with the grinding fluid conditioning, wheel dynamic balancing, online dressing, online grinding wheel control, grinding wheel control, grinding wheel control, grinding wheel control, and other functions, to achieve the highest efficiency. The crankshaft production line grinder is equipped with independent motion control functions, grinding fluid adjustment, grinding wheel dynamic balance, online dressing, online measurement and automatic loading and unloading auxiliary functions, realizing high efficiency and precision processing of crankshafts.
Moresuperhard CNC servo grinding machine for crankshaft processes automobile crankshafts: roundness of 2-4μm, cylindricity of 3-5μm; CNC follower camshaft grinding machine processes camshafts: cam contour ≤0.02mm, adjacent cam eccentricity error: ±6′; CNC follower eccentric shaft grinding machine processes RV gearbox eccentric shafts: roundness of 1-1.5μm, eccentricity error of ≤0.005mm. 0.005mm.