1.1Grinding method of integral blade disc CNC abrasive belt
1.2.3 Grinding of blade roots of integral blade discs
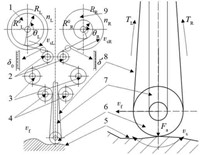
Fig. 1 Schematic diagram of new belt grinding method
The new type of abrasive belt grinding winds the abrasive belt 8 on the storage wheel 1, the take-up wheel 9, the transition wheel 2, the tension wheel 3, the wrap angle control wheel 4 and the contact wheel 6 and other wheel systems, through the grinding head to contact the rod 7 Control the contact pressure Fa between the abrasive belt and the workpiece surface 5, under the action of the grinding feed speed vf, the storage pulley and the winding pulley move synchronously, and under the condition that the pulley radius RL and RR continuously change, pass the control The synchronous movement speeds nL, nR and the rotation angles θL, θR ensure that the belt synchronous linear velocity vsL and vsR and the belt tension TL and TR are the same, thereby forming the belt reciprocating linear velocity vs. After completing a grinding cycle, the used abrasive belt is wound on the reel by the reel drive motor, and the new abrasive belt is transported to the profile grinding area by the storage reel drive motor.
The grinding process of the abrasive belt on the blade surface of the integral blade disk is shown in Figure 2: The contact rod of the grinding head forms a constant angle φ with the surface of the workpiece, and the contact wheel supports the abrasive belt and clings to the integral blade under the action of the grinding contact pressure Fa The disc blade profile; the belt drive roller drives the belt at a constant linear speed vs. at the same time, the grinding head performs a feed motion at a speed vf to realize the grinding of the belt on the blade surface.
The new type of abrasive belt grinding has the following advantages for the precision grinding of the entire blade disc: (1) The movement of the wheel system is driven by the storage wheel, and the belt is continuously updated automatically; (2) Under the joint action of the wheel system The abrasive belt can produce a certain rate of grinding motion. Under the condition that the workpiece only performs feed motion, the rapid accumulation effect of the abrasive belt micro-cutting is used to achieve efficient removal of the milling residual layer; (3) The contact rod through the grinding head Achieve pressure control to adapt to the deformation of the grinding process. In addition, the loss of the abrasive belt per unit polishing area of the whole blade disc is low (generally 3 to 5 mm/cm2), and a roll of abrasive belt (200 to 300 m) can meet the processing needs of the entire blade disc [13].
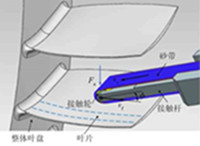
Fig. 2 Belt grinding blade surface of integrated blisk
1.2 Full-face grinding analysis of integral blade disc CNC abrasive belt grinding
1.2.1 Grinding of the blade surface of the integral blade
The space between the blades of the whole blade disk is narrow. When the abrasive belt is in contact with different cross sections of the blade shape during the grinding process, the contact rod is likely to collide with the blade and interfere with it. In order to ensure that the change of the radius of the blade curved surface is satisfied in the width direction of the belt contact, the radius of the contact wheel and the width of the contact wheel and the belt are minimized. The grinding process of the blade surface of the whole blade disc is shown in Figure 3. The curvature of the blade surface of the whole blade disc changes greatly. In order to reduce the number of commutation of the grinding head during processing, reduce the effect of motion accuracy error on the accuracy of the surface, improve the processing efficiency, and ensure the smooth transition of the profile to the edge during processing In the longitudinal feed grinding mode, the grinding processing path is shown in Figure 4.
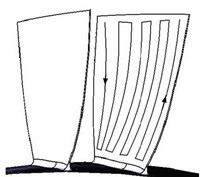
Fig. 3 Profile grinding blades Fig.4 Grinding track on blade
on integrated blisk surface
1.2.2 Grinding of blade edge of integral blade
The curvature of the blade edge of the whole blade disc changes the most, and it is easy to deform during grinding resulting in a discontinuous surface. However, due to the relatively wide edge of the blade disc, there is little interference between the grinding head and the blade. In the grinding process, on the premise of satisfying the machining efficiency and accuracy of the blade disc, the elastic characteristics of the abrasive belt grinding are used to optimize the grinding parameters, determine the reasonable walking step and step length, and reduce the walking step and step The influence of the length on the profile accuracy, so that the blade edge profile accuracy meets the design requirements. The grinding of the blade edge of the blade disc is shown in Figure 5.
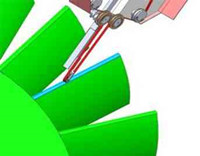
Fig. 5 Grinding blade edge of integrated blisk
The overall blade disc grinding device adopts Siemens 840D CNC system. The CNC machining software is the self-developed abrasive belt grinding processing software system TBGS. This software has model import and extraction of the machined surface, tool position calculation and tool path generation, The functions of simulation processing, CNC code generation and transmission can complete the tasks of CNC processing code generation, simulation, and transmission of CNC codes to CNC belt grinders. It has the characteristics of high precision and stable system. During the grinding process, the whole blade disk is clamped on a high-precision rotating turntable by special tooling positioning. According to the blade profile data, it is controlled by a high-end CNC system to achieve fixed-point contact between the abrasive belt and the blade profile, while being controlled by synchronous motion , To realize the abrasive belt grinding of the whole blade disc.
The surface of the blade root (blade root) of the whole blade disc is composed of the blade body profile, the blade root fillet and the flow channel surface respectively. The radius of curvature is small (the minimum radius of curvature is 1.25 mm), the blade spacing is small, and the abrasive system has poor accessibility. During the polishing process, the grinding head contact rod easily interferes with the blade. Therefore, when grinding the blade root, try to reduce the rotation angle of the grinding head. The schematic diagram of the grinding of the root of the whole leaf disc is shown in Figure 6
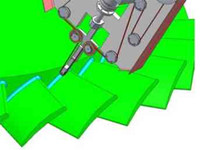
Fig. 6 Grinding blade root of integrated blisk
To achieve blade root grinding, axial force should be applied to the grinding. A new type of abrasive belt grinding method is adopted. The abrasive belt used in the processing has the characteristics of thin cloth base and large flexibility. It can cooperate with the contact wheel with a small radius of curvature that cannot be applied with conventional abrasive belts. Too small problem to realize the grinding of small radius of curvature of blade root fillet.
The analysis of the grinding process of the whole blade disc root belt is shown in Figure 7. In order to achieve the grinding of the blade root, the diameter of the contact wheel is 2.5 mm. At the same time, due to the small grinding space of the root, the grinding heat is difficult to radiate quickly. Therefore, an appropriate cooling method should be selected during the grinding process and the cooling should be reasonably configured Angle θ to achieve optimal cooling. The residual distribution of the leaf root of the whole leaf disc is uneven, and the residual at the center of the root is the largest. In order to ensure the accuracy of the blade root, the center part should be ground first, and then the two sides should be ground separately, which can effectively avoid the defects such as sharp angles.
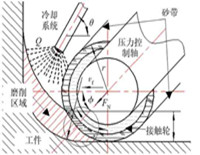
Fig. 7 Process analysis of belt grinding blade root