TP-4 is a four-axis precision cylindrical step grinder used as a pre-process production equipment after centerless grinding and before a five-axis tool grinder. The repeatability (R) is 2 µm and the positioning accuracy (A) is 4 µm.
TP-4 is a CNC four-axis precision external cylindrical step-difference grinder with roughing and finishing axes. It is suitable for grinding cylindrical materials and forming punches for grinding tools. It is a grinding production equipment between centerless grinding and five-axis tool grinding. It is suitable for grinding high-precision tool industry, mold industry, electronic parts and medical parts.
During grinding, the workpiece is supported by V-shaped support blocks and pressure wheels. The dimensional accuracy of continuous production can be controlled at 4 µm, the concentricity is less than 3 µm, the maximum grinding length is 330mm, the grinding diameter is 0.1‒20 mm, and the maximum aspect ratio is 350 times.
Grinding range φ0.1-20mm
Grinding length Max330mm
Aspect ratio 350*D
Concentricity <3μm
Double grinding wheel spindle design
Rough grinding and fine grinding are completed in one go
TP-4 CNC four-axis precision cylindrical step-difference grinder, using clamping stripping technology for grinding, with roughing spindle and fine machining spindle, capable of simultaneous grinding,
removing a large amount of material in the shortest time and providing excellent surface finish.
Mechanical structure of Cylindrical Step Grinding Machine
The main structure is a 4-axis CNC cylindrical grinder, equipped with an automatic 3-axis manipulator automatic loading and unloading system to achieve fully automated production. The grinding parts are designed with dual spindles, which are placed above the X and U axes respectively.
Double grinding wheel spindle
Working spindle
High precision, high stability
The working spindle head is equipped with high-precision bearings, which are extremely stable. The spindle and bearings are lubricated with grease to reduce wear and extend the life of the spindle.
The inner cone is BT40 design, which can be matched with a variety of clamping systems by installing pull bolts or pull rods.
Roughing and finishing grinding are performed simultaneously.
The workpiece passes through two grinding wheels and moves parallel to the axis, and roughing and finishing grinding are performed simultaneously. The moving axis is designed with a full closed loop through an optical ruler, and the grinding size accuracy can be controlled within ±2 um.
The roughing spindle is an HSK32E belt-type spindle with a rated power of 4 kw. The roughing wheel spindle angle can be adjusted to 0 degrees, 10 degrees and 90 degrees. To meet different processing needs, an upgrade to the HSK50 built-in spindle is provided, and the power is increased to 16 kw, which can perform a large amount of material removal, shorten the grinding time and improve production efficiency.
The finishing spindle is an HSK32E built-in spindle with a rated power of 4.2 kW. It can provide excellent surface finish and the best grinding effect when combined with different grinding wheel grits.
Feed processing mode
The W-axis and Z-axis of the mobile work head adopt a parallel superposition structure design. The high-precision parallel axis mechanism ensures stability during processing. The feed processing mode of the W-axis is "fixed" multiple grinding and forming, which is used for re-grinding production, and the Z-axis is "heart-moving" one-time grinding and forming, which is mainly used to produce drills, reamers, forming punches, tungsten steel fine needles and special cylindrical parts.
V-shaped support block and pressure wheel
During grinding, the workpiece is assisted by the V-shaped support block and pressure wheel, which can ensure the concentricity of continuous production is less than 3um.
Mechanical Features of Cylindrical Step Grinding Machine
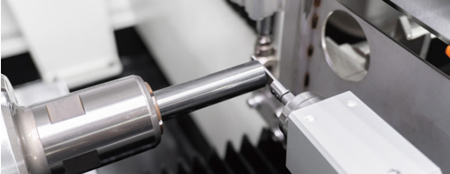
Front positioning function
The probe front positioning function records the clamping length of each workpiece before grinding.
Grinding wheel dressing device (finishing grinding wheel)
The machine is equipped with a manual finishing grinding wheel dressing device to ensure grinding accuracy and improve grinding efficiency.
Automatic loading and unloading system
The automatic loading and unloading system is equipped with a three-linear axis robot arm, which can automatically produce 24 hours a day, improve production efficiency, and significantly reduce the need for manpower. It can carry up to three trays, including two raw material trays and one finished product tray.
Maximum number of workpieces to be loaded
φ3-6mm: 600pcs
φ8mm: 240pcs
φ10mm: 180pcs
φ12mm: 160pcs
φ16mm: 96pcs
Control System of Cylindrical Step Grinding Machine

Human Machine Interface HMI
The main screen can display the axis coordinates, processing time, spindle load, grinding speed, grinding wheel speed, NC program and error messages.
The function keys on the right are links to various software, including Mode grinding mode selection, TP SMART software, PARA parameter setting, automatic loading and unloading system settings and Warmup warm-up
Grinding software
TP SMART Grinding Software
TP SMART software is the core function of TP-4 precision external cylindrical step-down grinder.
For end milling cutters, drill bits and other tool manufacturers, 34 built-in quick setting modules are available. Users can also use custom CAD mode to draw the required grinding shape, or use DXF file import function to do special forming step-down external cylindrical grinding, especially in the shape design of the forming punch part.
In the CAM part, the new material grinding or old material regrinding mode can be set; the grinding wheel selection includes three modes: single coarse grinding wheel grinding, single fine grinding wheel grinding, or coarse and fine grinding wheel simultaneous grinding. After inputting the workpiece speed, grinding wheel speed, grinding speed, coarse and fine grinding wheel spacing, grinding amount, and safe displacement distance in sequence, the grinding path can be quickly generated and a safe simulation can be performed. After confirming that the path is correct, the NC program is directly transmitted to the controller for grinding processing.
Integrated design of hardware and software of Cylindrical Step Grinding Machine
In terms of hardware, the operation box is designed with a 90-degree rotating shaft to meet the needs of operation in the work area and the material tray area; in terms of software, the self-developed human-machine interface highly integrates the FANUC controller, automatic loading and unloading system and grinding software TP SMART with the industrial computer, and the All in one operation concept makes the machine more user-friendly.
Applications of Cylindrical Step Grinding Machine
Shank diameter Ø4 mm
Front Ø2.878 mm; length 12 mm
Center Ø2.600 mm; length 14 mm
Magnification 1X (Nikon microscope)
Shank diameter Ø4 mm
Front Ø0.1 mm; length 35 mm
350 times aspect ratio
Magnification 5X (Nikon microscope)
Grinding wheel D64 / Grinding wheel SDC 1500
Cycle time: 46 sec
Surface roughness: Ra 0.12 μm
Controller: FANUC 0i-TF Plus
Software: TP SMART
Coolant: OELHELD ToolGrind TC-X 620