The orbital grinding is established a new standard of precision and flexibility to the finish grinding of camshafts or crankshafts, and other non-concentric applications. This technology is applicable wherever your grinding applications require high-speed interpolation and high stiffness.
The Applications of Moresuperhard Orbital Grinding Machine:
The orbital grinding machine, with its precision and versatility, finds invaluable applications in the automotive industry, particularly in the machining of crankshafts and camshafts. This advanced grinding technology enables precise and efficient shaping and finishing of these critical engine components, ensuring optimal performance and durability.
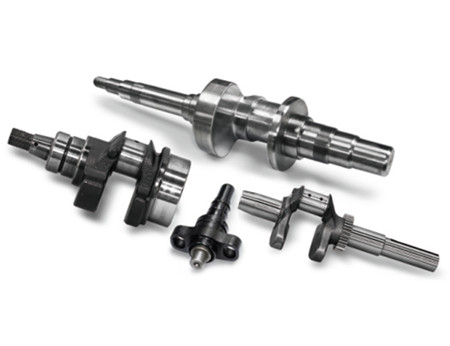
In the case of crankshafts, the orbital grinding machine excels in achieving highly accurate profiles and surface finishes for the crankpin journals and main bearing journals. By precisely removing material and maintaining strict dimensional tolerances, it ensures smooth rotation, minimized friction, and enhanced engine efficiency. Additionally, the orbital grinding machine can effectively correct any misalignments or deformations that may occur during manufacturing processes, thereby optimizing the performance and longevity of the crankshaft.
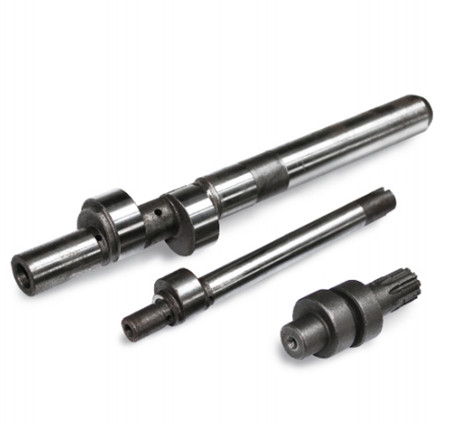
Similarly, for camshafts, the orbital grinding machine plays a crucial role in achieving precise and symmetrical cam profiles on lobes. This precision allows for efficient valve timing, improved fuel combustion, and reduced emissions. The orbital grinding machine's ability to accurately shape and contour cam lobes results in smoother valve operations, reduced wear, and increased engine power output.
Advantages of Moresuperhard's Orbital Grinding Machine:
·The CNC dual-axis interpolation linkage is adopted, and the closed-loop feedback control of the grinding wheel feed axis (X axis) and the workpiece rotation axis (C axis) is used to realize efficient fine grinding of crankshaft workpieces.
·Grinding wheel spindle: dynamic and static pressure liquid suspension electric spindle, high rigidity, high speed, low vibration and high grinding force.
·The working head adopts high-precision DDR rotary motor, high torque, high positioning accuracy
·Ring linear motors can provide greater instantaneous thrust than mainstream parallel linear motors, can offset the vibration when moving across magnetic poles, and run more smoothly
·Operation interface: Human-machine interface developed based on windows, graphical software can edit special-shaped contours online, making the operation easier