Solutions for Large Area Polishing and Grinding:
Grinding is generally used in various surface finishing processes. In fact, there are two definitions of grinding in China: one is free abrasive grinding, the other is abrasive disc grinding; This is called micro grinding method.
Grinding is a process method of micro-processing. With the help of grinding tool and abrasive (a kind of free abrasive), grinding produces relative motion between the machined surface of the workpiece and the grinding tool, and applies certain pressure to remove the tiny surface convex layer from the workpiece, so as to obtain very low surface roughness and high dimensional accuracy, geometric shape accuracy, etc. In mold manufacturing, In particular, precision die-casting moulds, plastic moulds and automobile covering moulds with high requirements for product appearance quality are widely used.
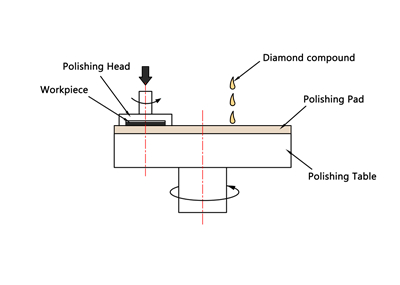
By replacing the original process with fixed abrasive tools, the manufacturing process can be shortened, thus reducing the manufacturing cost and reducing waste. The metal grinding wheel for fixed abrasive polishing is suitable for polishing high brittle materials such as ceramics. By fixing the diamond abrasive grains, the grinding wheel achieves a leap in machining efficiency and helps to improve the working environment.
Comparison of polishing effects of free and fixed diamond abrasive:
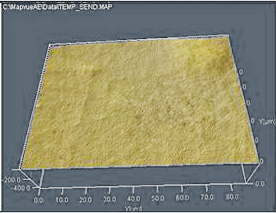
Glass polishing has a long history. It uses chemical or physical methods to remove pits, crack layers, scratches and other defects on the surface to improve the transparency and refractive index of glass. Glass materials are more and more widely used, such as computer hard disk glass substrate, thin film storage disk, laser crystal, and so on. The polishing methods used for different materials and requirements are also different. Abrasive polishing is widely used for its safety, wide application range, long service life, environmental protection and high polishing quality.
The traditional polishing process adopts the free abrasive polishing method, which is characterized by using the mechanical and chemical action between the polishing pad, the polishing fluid and the workpiece to complete the material removal. This process is highly dependent on the polishing fluid, such as the pH value of the polishing fluid, the type, concentration, particle size, particle dispersion and stability, etc, At the same time, a series of machining defects caused by the uncontrollable movement of abrasive particles in polishing, as well as the diamond particles left by the blunt polishing pad and the dressing after glaze, all affect the polishing effect.
In terms of economic benefits and environmental protection, fixed abrasive polishing( FAP) represent the development direction of flattening technology, especially the consolidated abrasive chemical-mechanical polishing technology in chip processing. FAP polishing technology uses self-made diamond consolidated abrasive polishing pad to polish mobile phone panel glass, and compares its material removal rate and workpiece surface quality with free abrasive polishing. The fixed abrasive polishing pad can realize the self-repair function in polishing, avoiding the defects on the workpiece produced in free abrasive polishing and the process complexity brought by diamond polishing ring; At the same time, deionized water is used as polishing fluid in FAP. There is basically no pollution of polishing fluid to the environment, and abrasive particles are consolidated and can be fully utilized to ensure the uniformity of material removal. Therefore, hydrophilic FAP has important economic and social benefits in terms of use cost and environmental protection.
Moresuperhard Solutions for Large Area Polishing and Grinding:
1. Diamond Lapping Discs:
► Bonded: resin bond, electroplated bond
► Model: 1a2
► The grain size up to
#15000
Suitable to grinding gemstone, jewelry, glass, rock, carving knife, etc…
These diamond discs are one of the finest discs manufactured for Hobby, Lapidary, Glass applications
The diameter flat lap wheels have a high density quality diamond coating.
They are absolutely flat and parallel to meet the most exacting faceting requirements.
Use the fine grit diamond lap pad to smooth and shape pieces and create polished flat surfaces
When used as part of a multi-stage grinding and polishing process it's easy to create smooth finished edges with a professional look.
2. Polyurethane Lapping/Polishing Pads
A
polishing pad is a thin disc of fabric or synthetic adhered to the flat surface of a polishing plate. It is used to produce the highest quality scratch free reflective surface finishes using diamond abrasive or chemical polishing agents. Polishing with a pad is considered a “soft polishing” technique because pad materials always have some amount of compliance. The thickness and hardness of the pad determines the compliance. Thicker, softer pads allow the components to sink down into the pad, which produces a radius at the contact edge circumference.
► Polishing and finishing of glass, LCD/LED substrates, precision optics, hard disk, metal and semiconductor wafer surfaces
► Model: MSH-66, MSH-77, MSH-13, MSH-LASER, MSH-46
► Thickness: 0.02" (0.508 mm) - 0.20" (5.08 mm)
With a global development strategy and comprehensive multilingual business departments, Moresuperhard keeps an eye on the latest developments in the global grinding industry and is committed to providing high-quality and efficient grinding products and services to our customers worldwide! We also accept customized orders to suit your needs.
If you have any questions about
Large Area Polishing and Grinding, please feel free to contact us! You can leave us your questions below, and we will contact you as soon as possible!