What is the current development of resin diamond grinding wheel?
With the development of artificial diamond industry and resin diamond grinding wheel in the field of grinding and polishing widely used, diamond grinding wheel special resin has also made development, successively appeared
phenolic resin,
DIALOK939P resin (actually a kind of phenolic resin and phenolic alkyl resin mixed resin) and
polyimide resin, etc. But compared to the diamond grinding wheel special resin, resin diamond grinding wheel special filler development is relatively slow and did not cause people's extensive attention.
What are the disadvantages of resin diamond grinding wheels?
The practice has proved that the resin diamond grinding wheel in use of the following shortcomings: because the resin heat-resistant temperature is not high and low heat transfer efficiency, grinding wheel in the use of the process, diamond particles around the resin due to grinding heat can not be timely dissipated, and was prematurely scorched or charred, resulting in diamond particles do not fully play a role and prematurely fall off, its utilization rate is greatly reduced, about 70% of diamond particles almost did not participate in the Grinding role and prematurely fall off, the performance of the grinding wheel is not wear-resistant; when the number of tools into the large, grinding generated by the local high temperature, resulting in the grinding wheel often appear smoke or cracking and other phenomena. Therefore, the resin bond diamond grinding wheel and metal bond diamond grinding wheel compared, because of its heat transfer heat dissipation effect is poor and resin is not heat-resistant, so its wear resistance is not good.
How do we enhance the heat transfer and heat dissipation effect of the resin diamond grinding wheel and prolong its service life?
The method to enhance the heat transfer and heat dissipation effect of the resin diamond grinding wheel are as follows:
Using powder filler with high thermal conductivity instead of copper powder as heat transfer and heat dissipation filler to manufacture resin diamond grinding wheel. The powder filler with high thermal conductivity can also replace the oxide powder filler in the resin diamond grinding wheel, and the manufacturing method of the grinding wheel is the conventional resin diamond grinding wheel production method.
What types of resin diamond grinding wheel do we have?
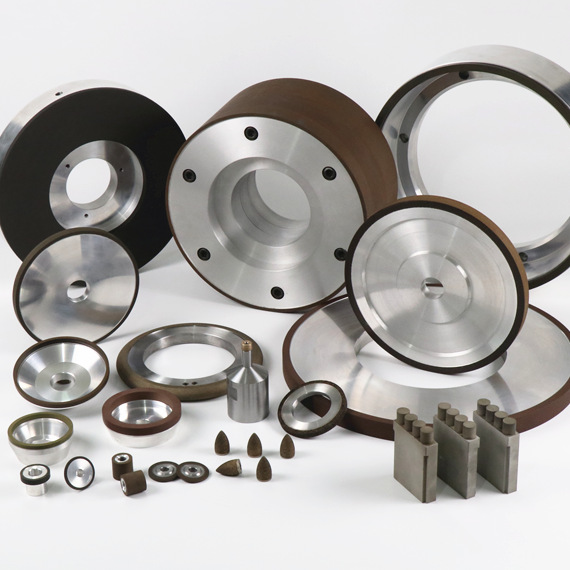
► Model: 1A1R, 1A1, 3A1, 1V1, 4A2, 4BT9, 6A2, 11V9, 12A2, 14F, etc
► Workpiece Materials: grinding tungsten carbide cutting tools, ceramic , magnetic materials, silicon , sapphire, glass , quartz and HVOF carbide coated,PCD, PCBN, etc
► Applicable Industry: carbide inserts (cnc tools), carbide circular saw (woodworking tools), Thermal Spraying Coated, Silicon Wafer Grinding, etc
If you encounter any problems in the process of using
Moresuperhard's diamond grinding wheels, please contact us in time. At the same time, we also welcome all customers to communicate and exchange with us!
---EDITOR: Jackie Wang
---POST: Jackie Wang