Moresuperhard provides
diamond cutting blade saws,
resin diamond lapping discs,
polishing pads and
diamond polishing paste and diamond compound for metallographic grinding and polishing. And metallographic analysis in the field of materials research occupies a very important position, and it is one of the main means to study the internal organization of materials.
What is Metallography?
Metallography is simply by looking at metal materials to identify and speculate on the properties of a metal material, so that we know in advance which material can make a sharp sword, which material can make a soft spring, so that according to the work tasks undertaken by the machine parts and the working environment in which the parts are located, a reasonable choice of different properties (mainly including material strength, hardness, plasticity, toughness, high-temperature resistance, corrosion resistance, etc.) of the material, so as to effectively improve the reliability and service life of machine parts.
Why we need metallographic sample making?
Metallography can be expressed as a branch of materials discipline with the help of microscopy to study and characterize the microstructure of materials. The natural surface of the metal is very rough, and it is difficult to directly see its internal organization, except for some very special cases such as fracture observation, which generally need to be observed on the surface treatment of the object. The purpose is to be able to see the internal organization under the microscope. The process of processing the observed object is metallographic sample making.
What is the process of metallographic sample preparation?
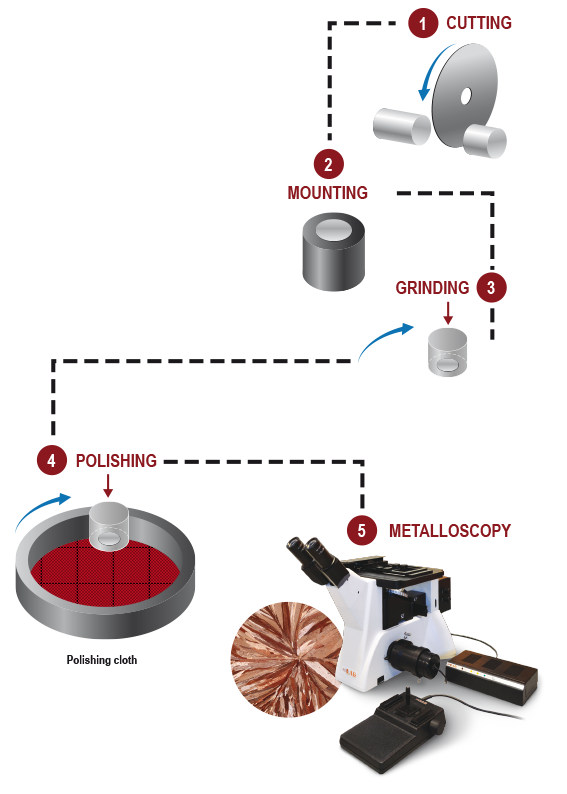
Sampling
To obtain a flat surface with as little distortion as possible in order to proceed quickly and easily to the next step, we generally use a combination of
diamond cutting blade saws and
diamond compound to process the sample, which causes the least damage compared to the time spent. While working, the coolant flushes the wheel to avoid thermal damage to the sample caused by frictional heat.
Rough grinding
The general material is coarsely ground with a grinding wheel. The operation should use the side of the grinding wheel to ensure that the specimen is ground flat. It should be noted that the contact pressure should not be too large at the same time should be constantly cooled with water to prevent the internal organization from changing due to temperature rise. After the rough grinding is completed, the outer edge of the specimen should be chamfered to avoid pulling the polished material apart during the subsequent process.
Fine grinding
The purpose of fine grinding is to eliminate the deep and coarse grinding marks left by rough grinding and to prepare for polishing. Fine grinding itself includes multiple operations, generally in accordance with the diamond grinding disc grit from coarse to fine order. At present, the mainstream fine grinding method is wet mechanical fine grinding, fine fine grinding is generally in order from the W40, one by one to replace the fine one grinding disc push grinding. Each change of the next fine grinding disc, the direction of the grinding surface should be rotated 90 °, in order to observe whether the last grinding marks are worn off. In the fine grinding of softer metallographic specimens, such as aluminum, magnesium, copper and other non-ferrous metals should be coated with a layer of lubricant on the sandpaper, which can prevent the abrasive particles embedded in soft metal materials, while reducing the surface tearing phenomenon.
Polishing
The purpose of polishing is to remove the abrasive marks left by the fine grinding on the metallographic specimen, and become a flat and faultless mirror surface. We generally use polishing pads or with some polishing paste or compound to polish the sample. Polishing results depend largely on the quality of the first few processes, so before polishing should be carefully checked whether the grinding surface abrasion marks are single direction and uniform.